History
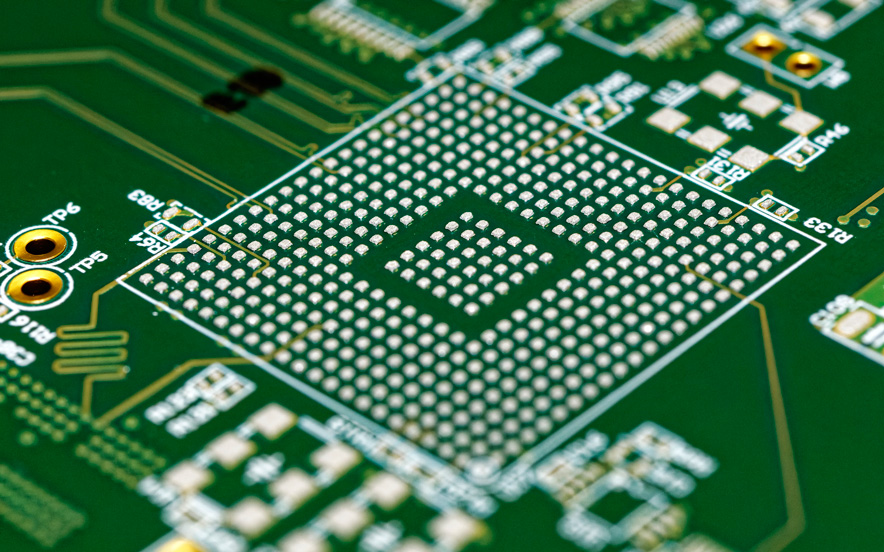
The TAUBE ELECTRONIC company has developed steadily since it was founded in 1986 and adapted to changes in the market. The most important events of the past 30 years are recorded here in retrospect:
2024
- Investment in new Keyence VHX-7000 digital microscope incl. 3D measurement capability
2023
- Investment in new EFA inspection system
2022
- Investment in new X-ray inspection system Quadra7 from Nordson/Dage
2021
- Inclusion of Rainer Taube’s proportional dimensioning concept in the IEC 61188-6 series of standards
2020
- Investment in 2 pick and place machines Juki RS1R for components up to 0201 metric
2017
- Certification of ESD protection in our production according to IEC / EN / DIN 61340-5-1
- Expansion of the equipment with Fischerscope X-Ray XDV-SDD
2016
- Expansion of the equipment with stencil cleaning system CL410
2015
- Investment in Koh Young 3D Zenith AOI system
- Investment batch cleaning system CL900
- Processing of components of type 01005
2014
- Expansion of the equipment with second pick and place machine JUKI KE-2080
2013
- Expansion of the business premises with a focus on enlargement of the test area
- Expansion of the equipment with solder paste printer DEK Horizon 03iX
2012
- TAUBE ELECTRONIC GmbH becomes a training center for electronics technicians for devices
and systems
2011
- TAUBE ELECTRONIC celebrates 25th company anniversary
- The machine park is modernized and enlarged: acquisition of a second fine placer to expand the rework capacity;
- Investment in a new selective soldering system Seho PowerSelective with 2-fold solder bath
- Acquisition of an Ersascope 1 Plus
- Processing of µQFN components with a pitch of 350 µm
2010
- Susanne Taube took over the commercial management
- Processing of µBGA with a pitch of 400 µm
- Improvement of the reflow process: Investment in a VXS nitro 2100 reflow system from Rehm
- Participation in the RKW projects “Growth” and “Personnel Diversity”
- Own investigations for – minimizing voids in soldered joints
- Optimization of the lead-free wave soldering processes by using a top heater
2009
- Improvement of testing and rework possibilities through new X-ray inspection system GE phoenix micromex
- Increased flexibility in production: installation of the state-of-the-art Mydata MY500 stencil-less paste printing system
- Recertification of the production staff according to IPC-A-610D
- Installation of a local nitrogen generator especially for the selective soldering process
2008
- Installation of selective wave soldering system
- ESD Certification of production according to IEC/EN/DIN 61340-5-1
2007
- Design of a highly complex impedance controlled HDI rigid-flex multilayer with 14 layers and integrated impedance control coupons
- Processing of µBGA packages with 0.5 mm pitch on mini-BGA module with balling process
- Acquisition of a vapour phase soldering system
- Training and certification of all staff (except administration) according to IPC-A-610D
- Installation of a high-precision pick and place machine Juki KE-2060R for components from 0201 up to 75 mm x 75 mm
2006
- Start of the manufacturing of “Green” assemblies
2005
- Conversion of the sole proprietorship TAUBE ELECTRONIC, Rainer Taube into TAUBE ELECTRONIC GmbH
- Recertification of production employees according to IPC-A-610C
- Manufacturing of RoHS-compliant assemblies
- Commissioning of an automatic coating machine and an X-ray fluorescence spectroscopy system to check the RoHS conformity of components and assemblies
2004
- Expansion of the operating area to approx. 1000 m2.
- Conversion of production to lead-free assembly technology
- Jürgen Paape and Angela Lange qualified as CID + / FED designers
2003
- TAUBE ELECTRONIC is awarded “Component Manufacturer of the Year” for the second time
- Acquisition of an X-ray inspection system benchmate / phoenix x-ray
2002
- TAUBE ELECTRONIC is awarded the title “Assembly manufacturer of the year”
- Introduction of AOI (Automatic Optical Inspection) in assembly production
- Installation of the second pick and place machine HEEB Inoplacer HP
- Certification of Rainer Taube as IPC-A-610 Class A Instructor
- Training and certification of employees in production according to IPC-A-610C
2001
- Acquisition of a MIELE cleaning machine
- Implementation of the BGA reballing process
2000
- Expansion of the rooms to 750 m²
- Acquisition of a climate test chamber
- Discontinuation of software sales
1999
- Regular processing of BGA and micro-BGA packages
- Acquisition of an EKRA E1 stencil printer with vision system
1998
- Implementation of the BGA processing in the assembly production.
- Acquisition of an automatic placement machine HEEB Inoplacer HP and a FineTech Fineplacer for placement, soldering and desoldering of BGA, CSP and FlipChip
- Acquisition of a convection reflow soldering oven
1997
- Certification of the quality management system according to ISO9001
1996
- Combined project with FHG-IZM to develop a tool for the automatic checking of circuit boards, especially with MCM’s, for EMC and thermal problems
1995
- Reorganization of all processes and preparation for certification according to ISO9001
- Expansion of sales through agreement with Intergraph about VERIBEST PCB
1994
- Reduction of project lead times and increase in quality through our own project management tool for ULTIboard; Objective: just one redesign before series production
- Design and manufacture of an assembly with 0.4 mm pitch in SIPAD technology
1993
- Development of an EMC-safe conversion and distribution computer for KRONE REW
- Expansion of production after a positive assessment of the market opportunities for electronics service providers with full service
1992
- Development of a supplementary programme for ULTIboard for hierarchical PCB design
- Development of a DFX interface for ULTIboard
- TAUBE ELECTRONIC joins the newly founded association FED and is the member with the no. 0017
1991
- Multilayer design in the 4 GHz frequency range; 6ML rigid-flex printed circuit board for medical technology
- Production of a highly reliable multiprocessor system in a controlled production process according to IPC-S-815 on multilayers with individual numbering and micrographs for each PCB; subsequent assembly with exclusively MIL components, cleaning under MIL limits and coating
1990
- Establishment of a new business area: sales of printed circuit boards
- Design of a complex 6-layer graphics card with EMC test
1989
- Opening of a new business area: Sales of CAE software with ULTIboard from ULTIMATE TECHNOLOGY, the Netherlands
1988
- Design and assembly of SMD multilayers
- Layout and production of a highly reliable plug-in card multiprocessor system for KUNOW Elektronik Berlin, end customer CAMERON, circuit diagram input with ORCAD, layout with AUTOPCB (based on AUTOCAD)
1986
- Rainer Taube, who has many years of professional and practical experience in SMD design and assembly production, founds the company.
- The business areas of TAUBE ELECTRONIC are printed circuit board design and assembly production (especially SMD and HF);
layout realisation, initially using adhesive bonding technology; production of sample printed circuit boards including repro technology